Research Overview
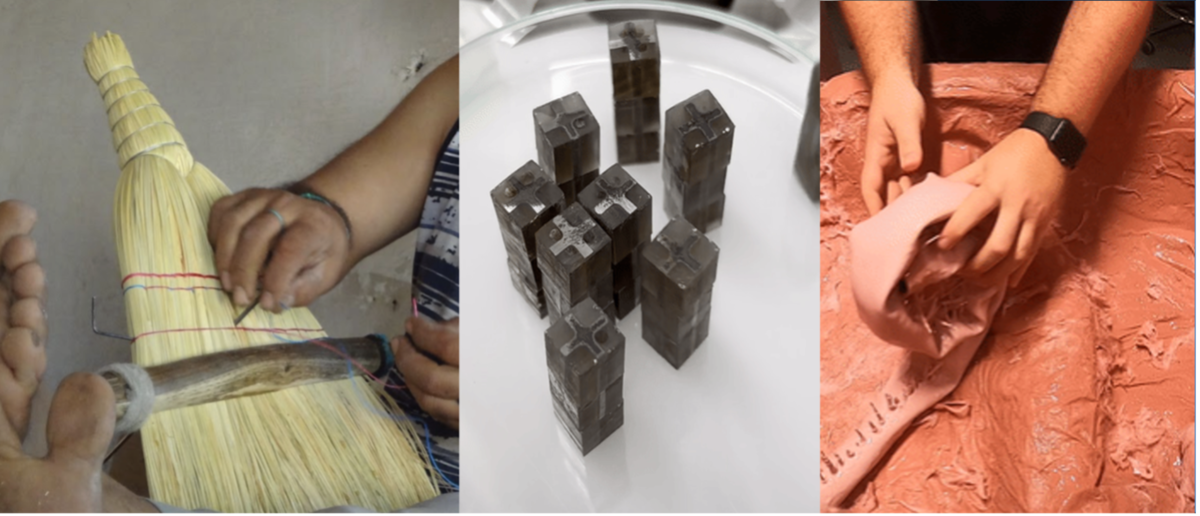
The research group, RoCoCo (Robotic Composites and Compositions), focuses on the design, fabrication, modeling, and testing of active composite metamaterials. The group develops adaptive and dynamic structural components for robotics applications, such as minimally-invasive surgical procedures, human-material interaction, and sustainable circular manufacturing.
Robotics promises autonomous machines that help us achieve difficult tasks not only in structured environments like factories, but also in unpredictable environments like oceans, cities, our homes, our bodies, and our blood vessels. For robots to succeed in these kinds of real-world situations, they need to be adaptable. The traditional approach to achieving adaptable mechanical behavior in robots involves high-quality actuators and sensors on custom prefabricated rigid parts made of metals or hard plastics, coupled with sophisticated control algorithms. However, this approach is not only computationally and physically expensive, but it also (a) is too bulky and rigid for some high-impact domains such as constricted areas inside of the human body and, (b) does not allow for easy and on-the-fly reconfiguration of the structural components.
Our research addresses this gap by developing dynamic composite material systems with actively tunable properties – such as stiffness, elasticity, and shape memory – to enable safe, adaptive, and versatile robot-environment and robot-human interactions. We work at the intersection of mechanics, robotics, materials, and design, benefiting from and contributing to sub-fields such as soft and underactuated robots, architected materials, modular robotics, granular matter, swarm robotics, and circular engineering. We take a hierarchical design approach across scales, from the composite material level to the device level. We combine a primarily experimental approach with theoretical and computational methods, to map our deep understanding of non-linear and temporally varient mechanical behaviors to sensing, actuation and control challenges in robotic material systems. We program adaptability and reconfigurability into our robotic components not just to enable more precise and versatile force and position control, but also to enable the circular reuse of robotic components, thereby promoting sustainable design practices. We aim to develop families of robotic composites that can help address key challenges in medicine, sustainability and human-technology interaction.
Upcoming projects:
Remote-controlled magnetic devices at the millimeter and micrometer scale for surgical procedures in hard-to-reach areas inside the human body. These devices will shape-morph and assemble in situ, perform precise delicate procedures by utilizing the tunable mechanical behaviors, and then re-morph or disassemble for easy removal.
Life-cycle design of robotic aggregates to enable circular sustainability, with the aim of replacing existing irreversible traditional fabrication techniques (such as forming through plastic deformations) with reversible structural phenomenon (e.g. jamming). This involves the development of new jamming actuation modalites uniquely suited for reuse, considering the impact and suitability of the newly-proposed life-cycles.
Metamaterial fabrication and design inspired by traditional craft techniques such as broom-making, basketry, and lacemaking. We aim to translate the generational know-how which is an essential part of our intangible cultural heritage into rational engineering design guidelines and frameworks.
Human studies involving physical interaction with active matter, focusing on incorporating dynamic changes in object properties such as stiffness or plasticity into human-machine interaction platforms such as interactive art experiences. These studies aim to provide insights to human-object interactions, specifically as robotic systems become more seamlessly integrated into our daily lives.